Whether you need to transfer a pencil drawing to a canvas, stick a custom vinyl on your water bottle, or iron a picture onto a throw pillow, there is a transfer paper that can help you. While all types of transfer paper are relatively easy to use, different crafts require different transfer methods and materials. Deciding what you want from your project will help you know what kind of transfer paper to get and how to use it properly.
A lot of people are familiar with screen printing, also known as silkscreen. However, today you can achieve similar results by using specialty transfer papers, films and vinyl, which can be used on inkjet or laser printers of other speciality equipment. Below, I'll list a few of the most popular and frequently used methods.
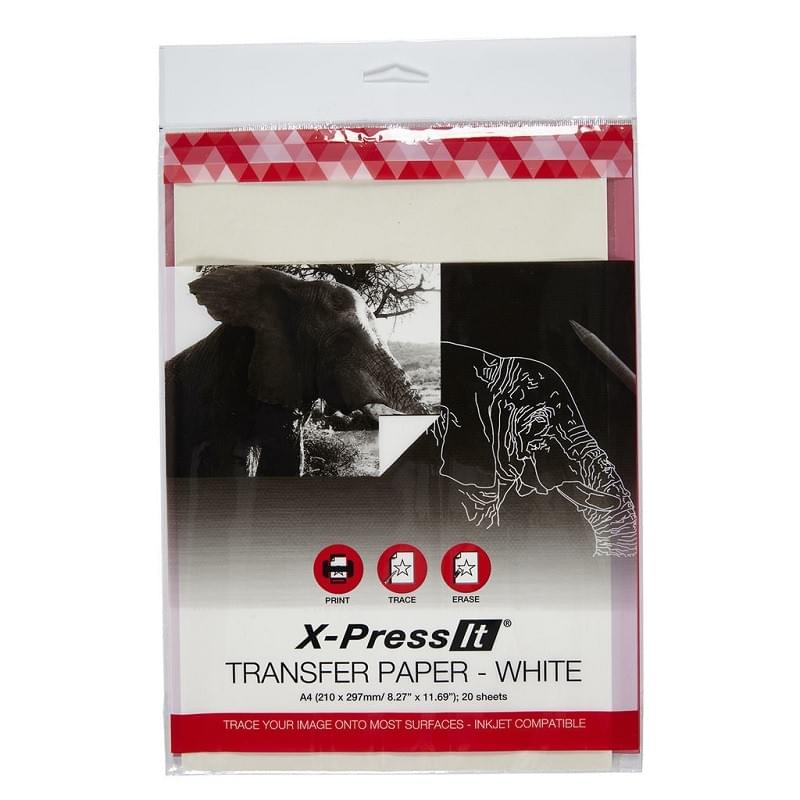
Inkjet Transfer Paper
This is the most used method for producing inkjet transfers for home use or for a small business. The process can be done using a normal inkjet printer and normal inkjet inks and involves transferring a graphic, image, text, logos, design, etc, onto specially coated inkjet transfer paper. Inkjet transfer paper is suitable for light and coloured fabrics, although the methods of application are slightly different.
When using this transfer method on white or light coloured fabric, the image needs to be printed in reverse onto the transfer paper. The printed image is then placed faced down onto the fabric and heat is evenly applied, either by home iron or heat press, to create a chemical process that allows the ink to bond with the fabric. Peel the backing paper away and the image will be left on the fabric. To further set the image to the fabric, place a piece of silicone paper over the image and re-heated it for just a few seconds.
For black or dark coloured fabric, the image should be printed onto the transfer paper (no need for reserve printing) that is specially designed for dark or multicoloured fabrics. You then peel the image off the backing paper and place it into the fabric. Place a piece of silicone paper over the image and apply heat. You can then remove the silicone paper and your image will be set.
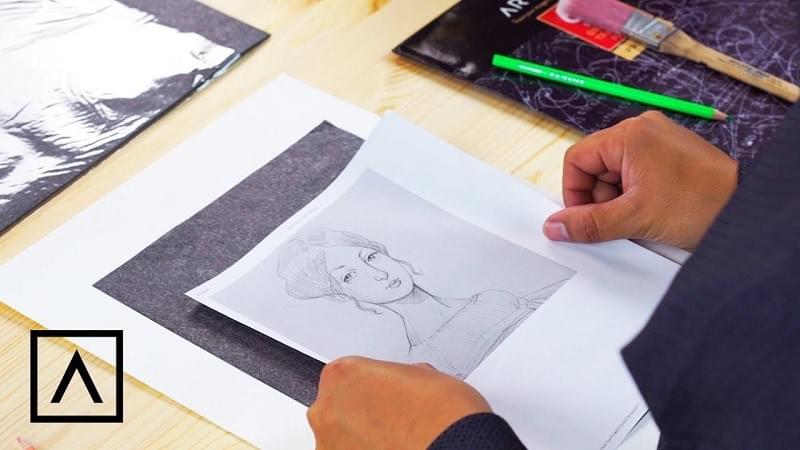
Graphite Transfer Paper
This is another great invention for artists. Graphite paper is similar to carbon paper, which was used a lot in the past for record-keeping purposes, but isn't used as often these days. If you're not familiar with the concept, to make an instant copy with carbon paper, you place it underneath the writing paper and a copy of what you write is transferred to the sheet below. Graphite paper works exactly in the same way but uses erasable graphite.
It's not recommended to use carbon paper for art-transfer purposes because it's coated with wax, making it difficult to erase. Graphite paper is a lot more cleaner to work with. It is greaseless, leaves behind less residue and is easy to erase. It's also available in different colours. When working with graphite paper, consider using a mechanical pencil to do the tracing as it always retains a sharp point. Make sure to trace all the contours of al; the objects, as well as all the shadows and highlights. You may also want to make a mark any time there's a colour change. The important thing is to make a mark noting every visual piece of information that you'll need to create your painting.
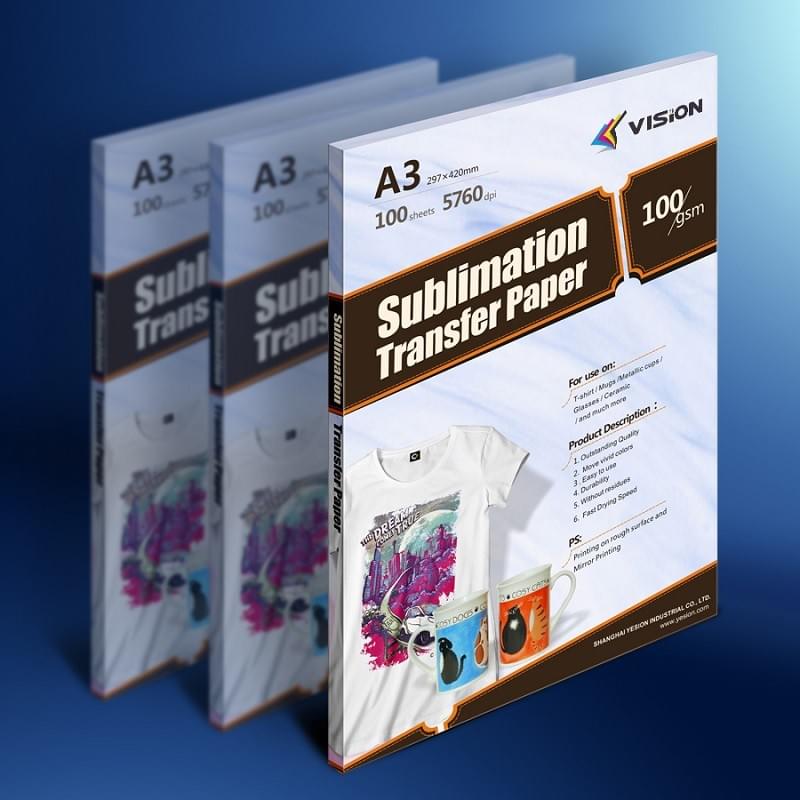
Sublimation Transfer Paper
With this method, the ink "sublimates" or become a gas without liquefying first. The process lays down varying amounts of main colours plus a clear coating onto the paper. The gas then solidifies on the page, resulting in full-colour images. The clear coat protects the ink from smudging during the heat stage. As the inks are transformed into a gaseous state, it penetrates the fabric (similar to a dye), making it permanent.
Sublimation transfer is suitable for use on polyester, polyester blend and other synthetic fabrics but shouldn't be used on cotton or cotton-based fabric. It can also be used to print other specially coated hard goods like mugs or promotional. However, the items need to be properly coated to accept sublimation inks.

Plastisol Screen Printed Transfer Paper
Also called hot-split or hot-peel, this transferring method leads to a finished product that is almost identical to screenprinting. The image is transferred into this transfer paper with the use of a screen printer and then transferred onto fabric with a heat press. The paper needs to be peeled off immediately after pressing, which in result, doesn't allow full ink saturation to occur. Still, the image is fully transferred and the fabric remains soft.
More cost-effective than sublimation, this transferring method still requires costly specialty equipment such as a screen printer and a heat press. Furthermore, plastisol printing limits the variety of colours you can use. It can be applied to any cotton, polyester or blend fabric.